PRINCIPE EVO 2.0
Patented, automatic, continuous belt screen changer for molten plastics (melt).
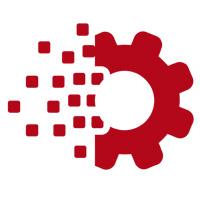
A simple and safe system – fully automatic operation
(operator involvement limited to the simple mesh roll replacement operation)
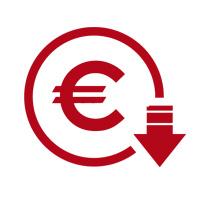
Low operating cost – Minimized scrap
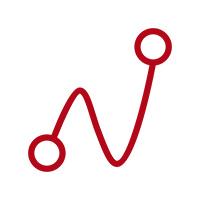
Increased productivity (non-stop production)
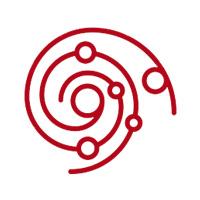
Easy scrap handling (used mesh)
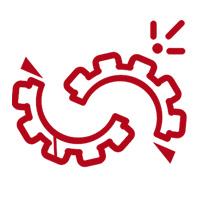
Spare parts and maintenance cut down to a minimum
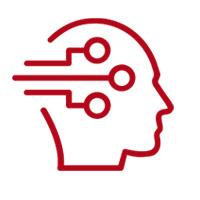
Testing, commissioning and after-sales service
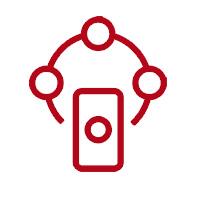
Remote assistance through tele-service
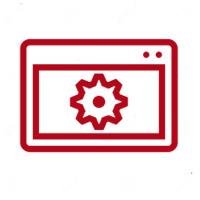
The implementation of Tandem software allows you to work with very high levels of contamination while ensuring extended mesh service life and increased durability of the mechanical components of the plant.
PRINCIPE EVO 2.0: WHAT IS IT?
It is the innovative, automatic, continuous belt filtration system designed to reduce operating costs and improve productivity of plastics extrusion plants for recycling and compounding.
The operator involvement is limited to the simple mesh roll replacement operation (approx. 5 minutes). This guarantees an autonomous non-stop production system – no process interruptions – 24/7.
PRODUCT BENEFITS
CONTINUOUS FILTRATION
PRINCIPE-EVO has been designed to ensure continuous-flow filtration processes so as to guarantee non-stop production while boosting productivity of plastics recycling and recovery plants.
OPTIMIZED PRODUCTIVITY
The fully automatic operation – controlling all mechanisms and managing every parameter via PLC – ensures a safe, stable filtration process while optimizing the productivity of the entire recycling line.
SAVINGS: SCRAP CUT DOWN TO A MINIMUM
Savings derived from the use of our automatic, continuous belt screen changer for molten plastics (melt) are the result of low operating costs combined with outstanding production efficiency and minimized scrap – following the introduction of two innovative patented systems: Evo-Block and Evo-Pulling.
EFFICIENCY
PRINCIPE-EVO has been designed to minimize operator involvement and downtime, improving performance without compromising the productivity of plastics recycling and recovery plants.
HIGHEST RELIABILITY
The fully automatic control of the screen changer mechanisms – which carry out the highly accurate mesh replacement operation – ensures the extreme stability of the process.
PROCESS STABILITY
The fully automatic control of the screen changer mechanisms, which carry out the mesh roll replacement operation with accuracy and precision, ensures the extreme stability of the process.
SAFETY AND SIMPLICITY OF OPERATION
Simple and safe system, given the linearity of the mechanisms to be controlled.
MESH ROLL REPLACEMENT
The operation requires no welding and is easily carried out. The roll service life (100 m) depends on the level of contamination of the filtered material.
HIGH QUALITY - LOW PRESSURE VARIATIONS
The optimized usage of filter surface areas ensures the precise control of pressure variations, which are minimal so as to avoid any alteration of the melt, thus guaranteeing the highest quality of the end product.
EASY SCRAP HANDLING
The filtration system, based on dirty filter mesh replacement, involves the shearing and scraping of the mesh at the outlet, for its disposal in an easy-to-empty container.
SCRAP MINIMIZATION
Substantial savings by minimizing scrap through optimized mesh usage, thus ensuring maximum performance of all filter surface area.
FULL CONTROL OVER THE CONSTRUCTION PROCESS
Our machines are entirely built in-house (except for heat treatments).
TESTING
Testing is carried out at our premises with the material supplied by our customer.
REMOTE ASSISTANCE
Through tele-service, we can intervene on the plants installed at our customers’ premises at any time and anywhere in the world, thus ensuring the effective techhnical support of our qualified personnel.